Systems Engineering
Table of Contents
Criteria 4
Work Plan:
Stage | Week | Task |
Prototype | 7 | 1. CNC cut prototype of top and bottom enclosure pieces from 2mm aluminum sheet. |
Prototype | 7 | 2. Evaluate prototype and adjust design if necessary. |
Production | 8 | 3. Update CNC cutting files based on prototype evaluation. |
Production | 8 | 4. CNC cut final top and bottom enclosure pieces from 2mm aluminum sheet. |
Finishing | 9 | 5. Sand all aluminum pieces for a smooth finish. |
Assembly | 9 | 6. Pop-rivet sides (left, right, front, back) and bottom of enclosure. Ensure proper alignment and placement of rivets for a strong and secure assembly. |
Electrical Design | 10 | 7. Design a wiring diagram for the enclosure components. Design the wiring diagram using the software Fritzing which has all the parts required |
Electrical Testing | 10 | 8. Test the wiring diagram for accuracy using a breadboard. Wire accordingly as per the diagram created in Fritzing and make any changes as required |
Assembly | 11 | 9. Install wiring and components inside the enclosure. Install the wiring into the enclosure and place the components ready to be coded |
Programming | Term 2 School Holidays | 10. Program the Arduino to meet project requirements. Program the Arduino using the Arduino IDE software to meet the specific requirements of the DAW Controller. |
Testing | Term 3 Week 1 | 11. Test the DAW Controller using a DAW such as Logic Pro to ensure code works along with all the wiring |
Work Plan Tasks 1-4

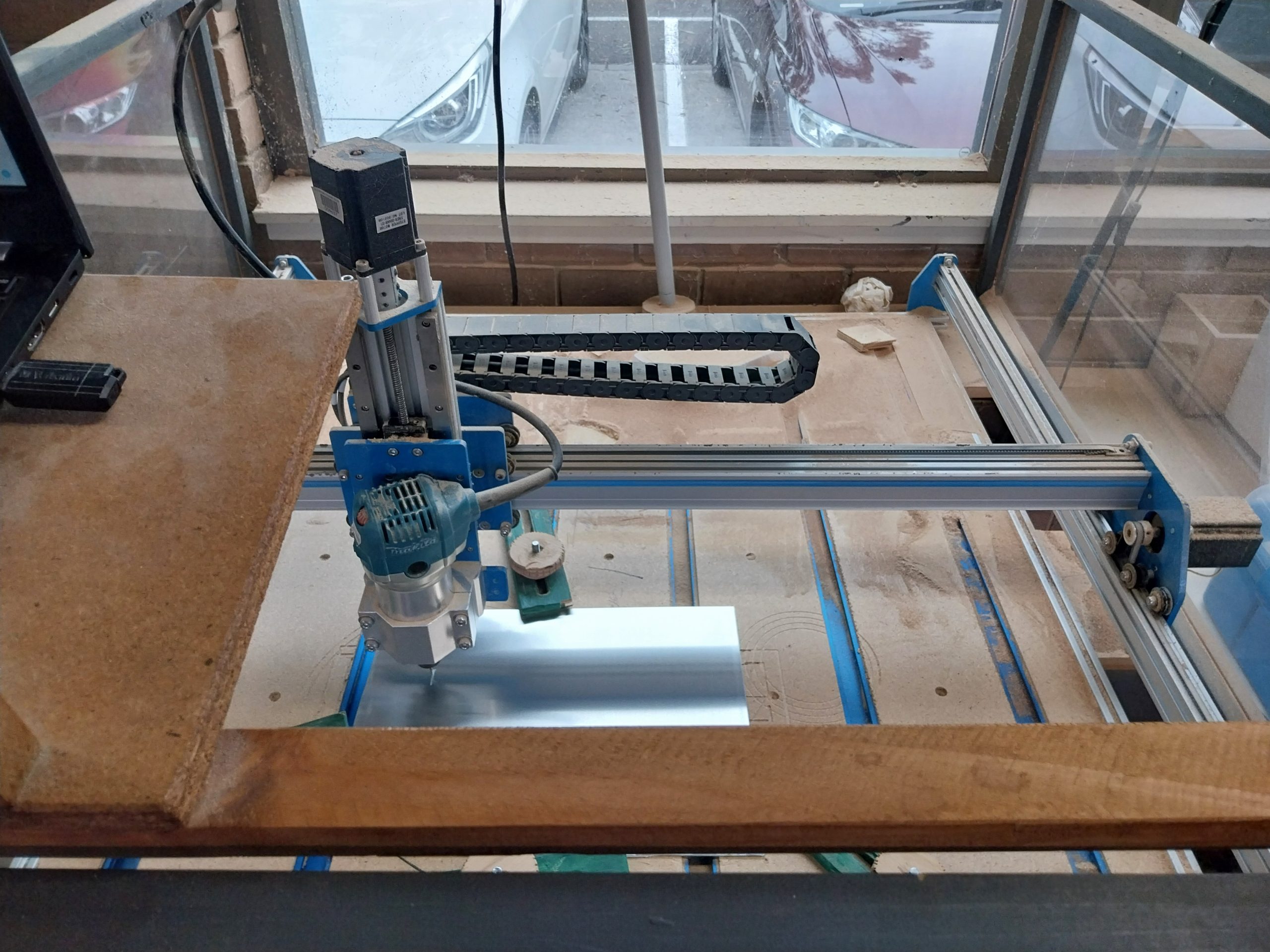



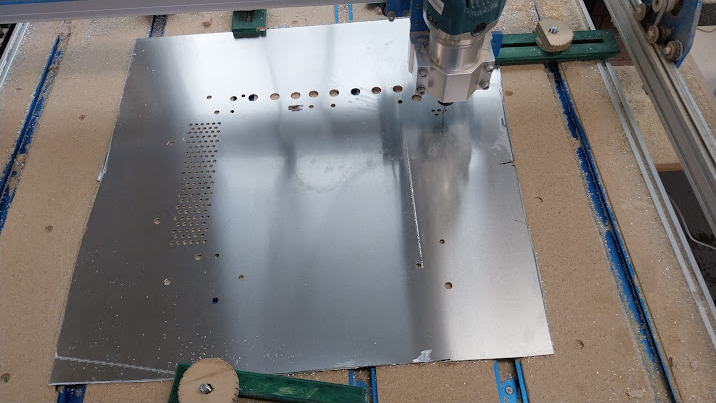
Issues:
As a result of incorrect settings with the workspace in Easel, the CNC router had cut completely through the aluminium sheet resulting in a hole and waste of aluminium. Due to that, I routed on Wood instead to get accurate settings instead of wasting more aluminium and not having any left. The design worked on wood which I then decided to route the outline of Anirudh on a small piece of aluminium to test. With it working, I continued working on other aspects of the project.
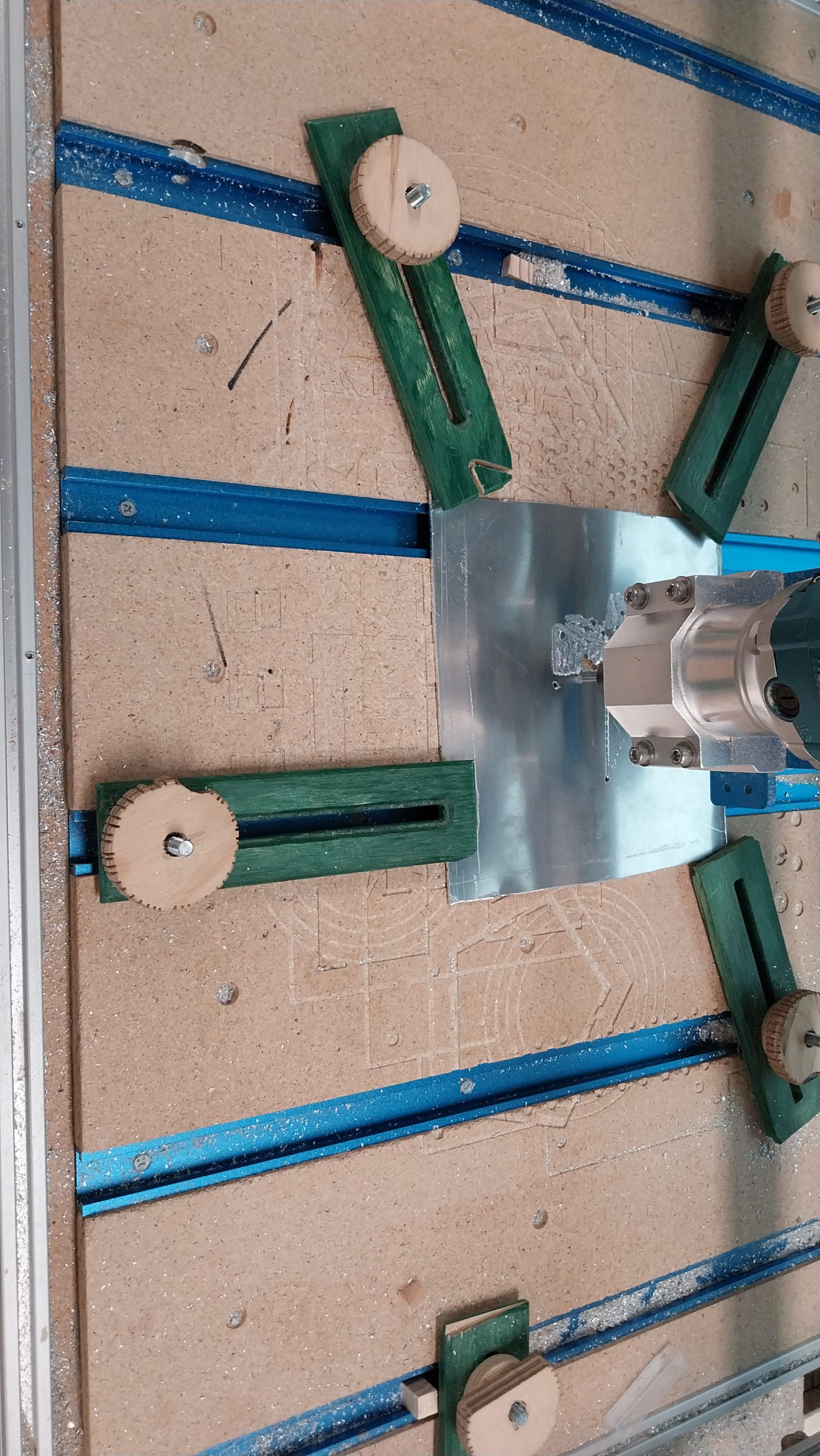
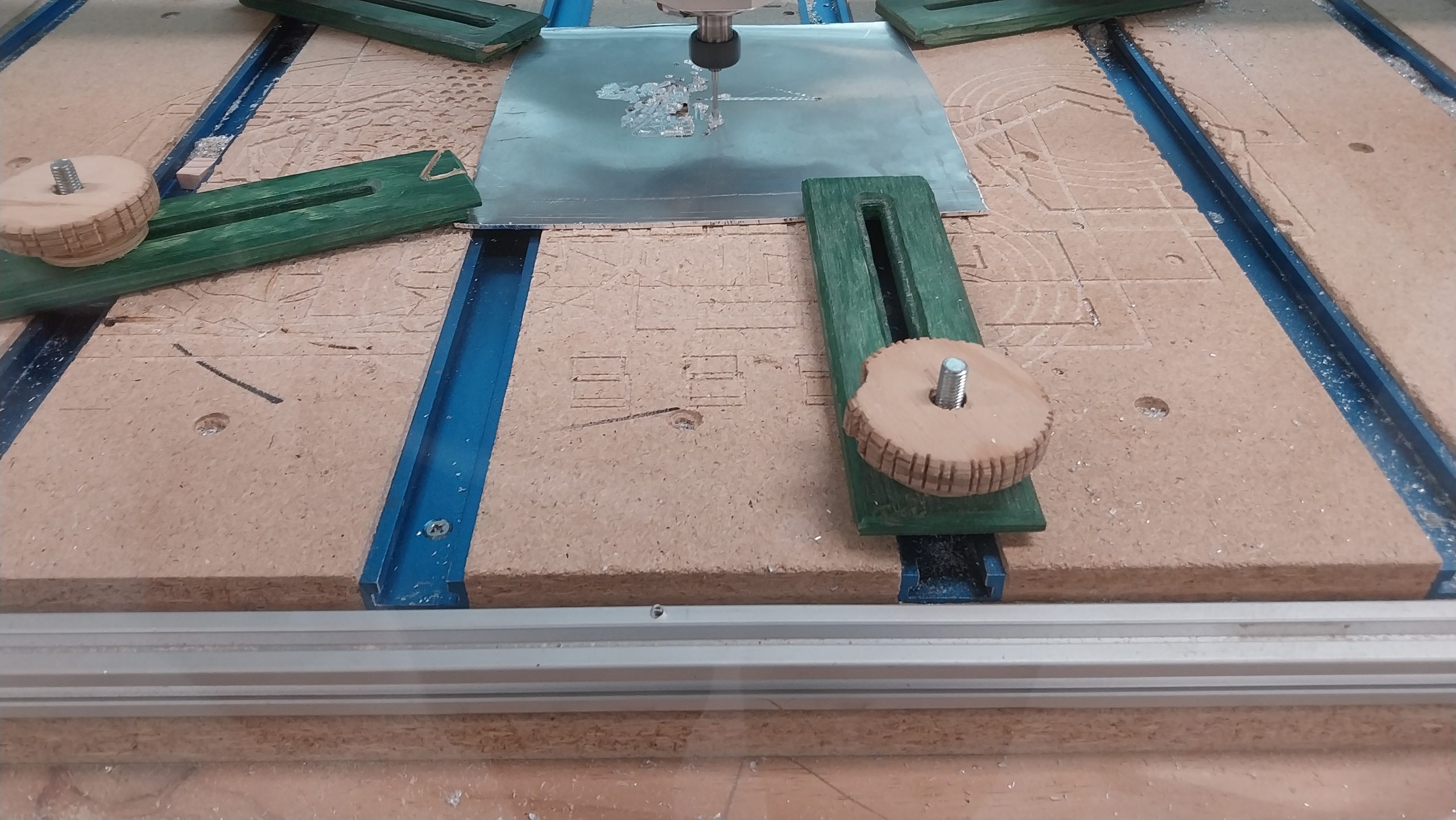
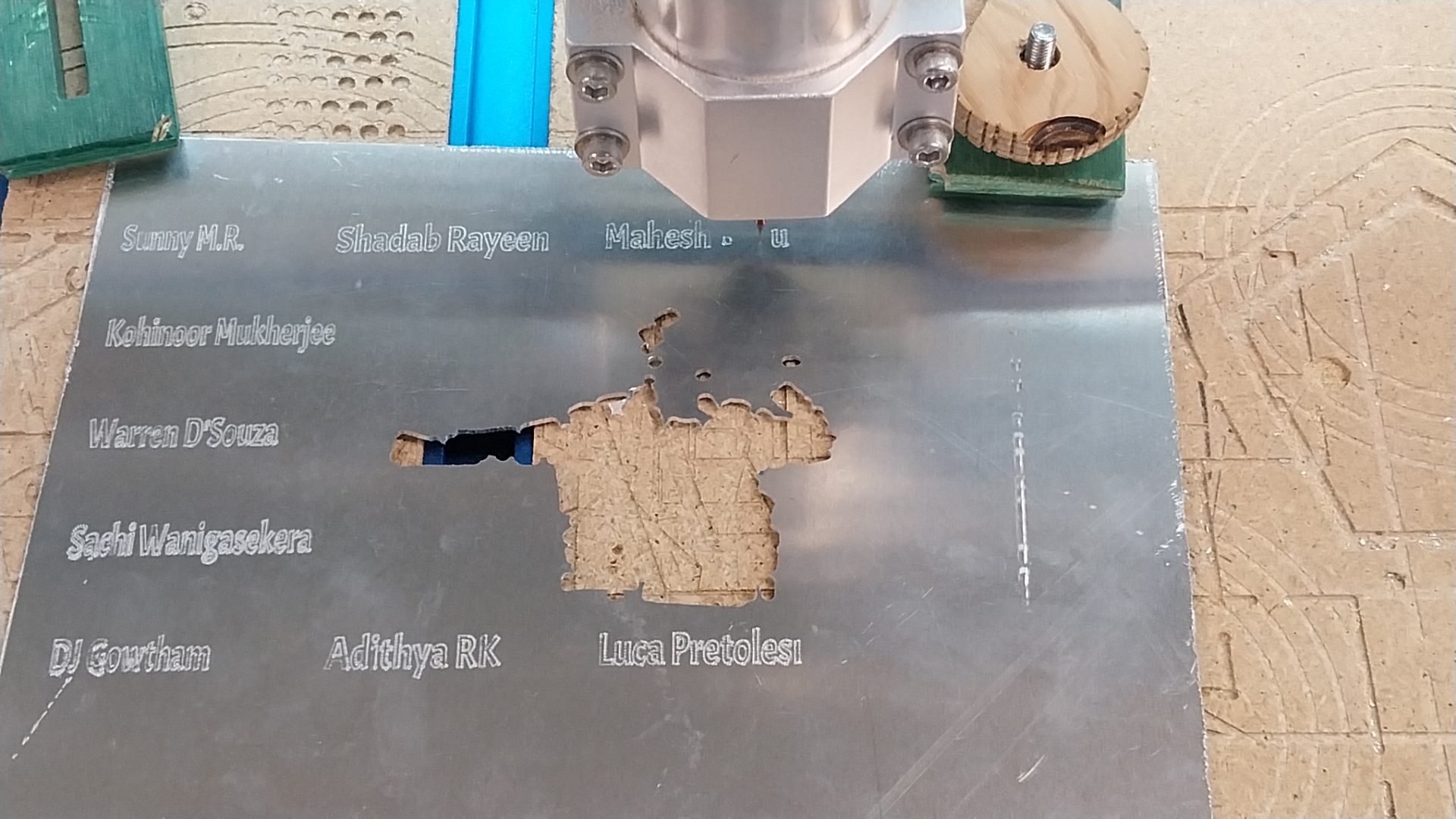
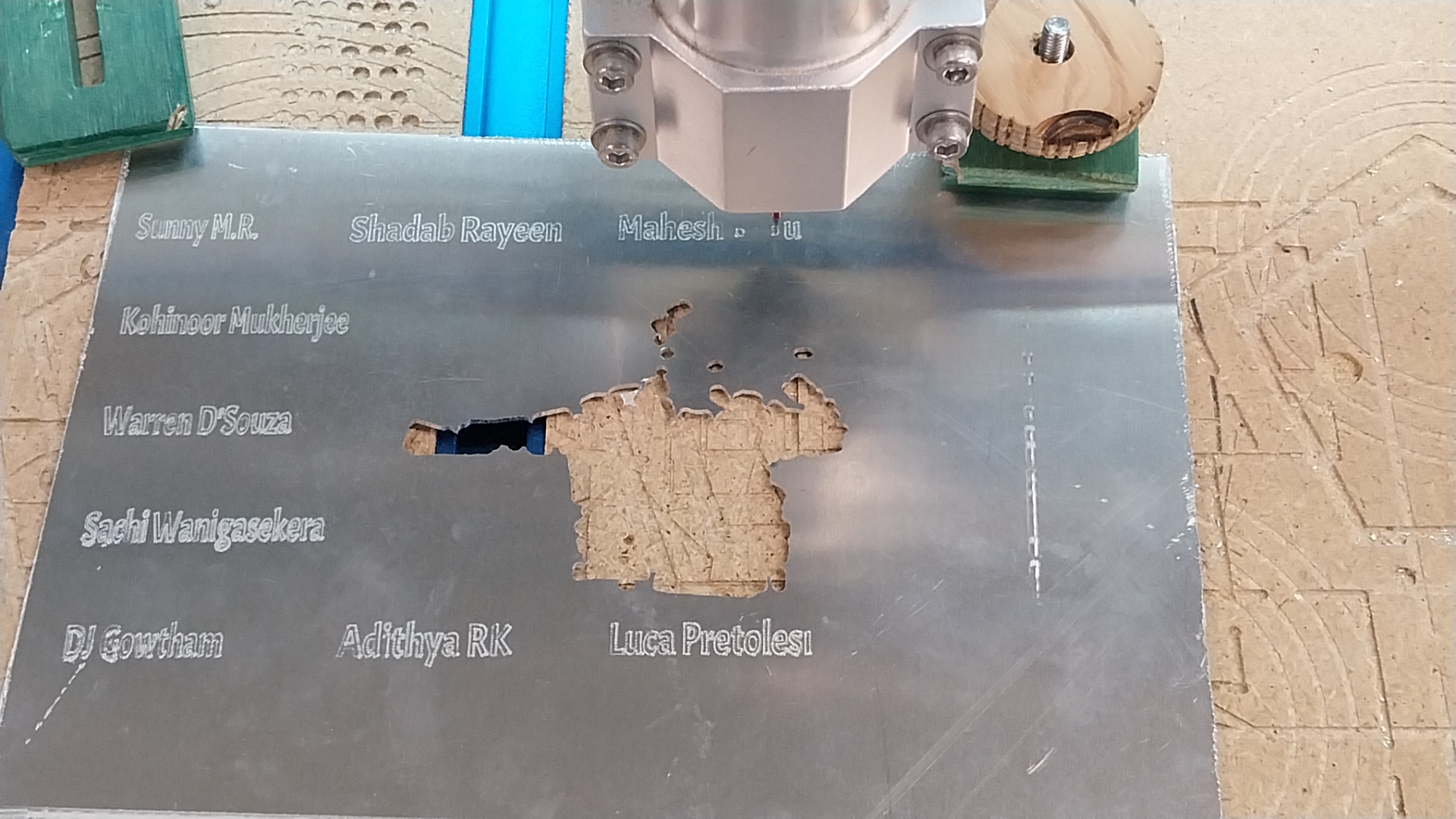
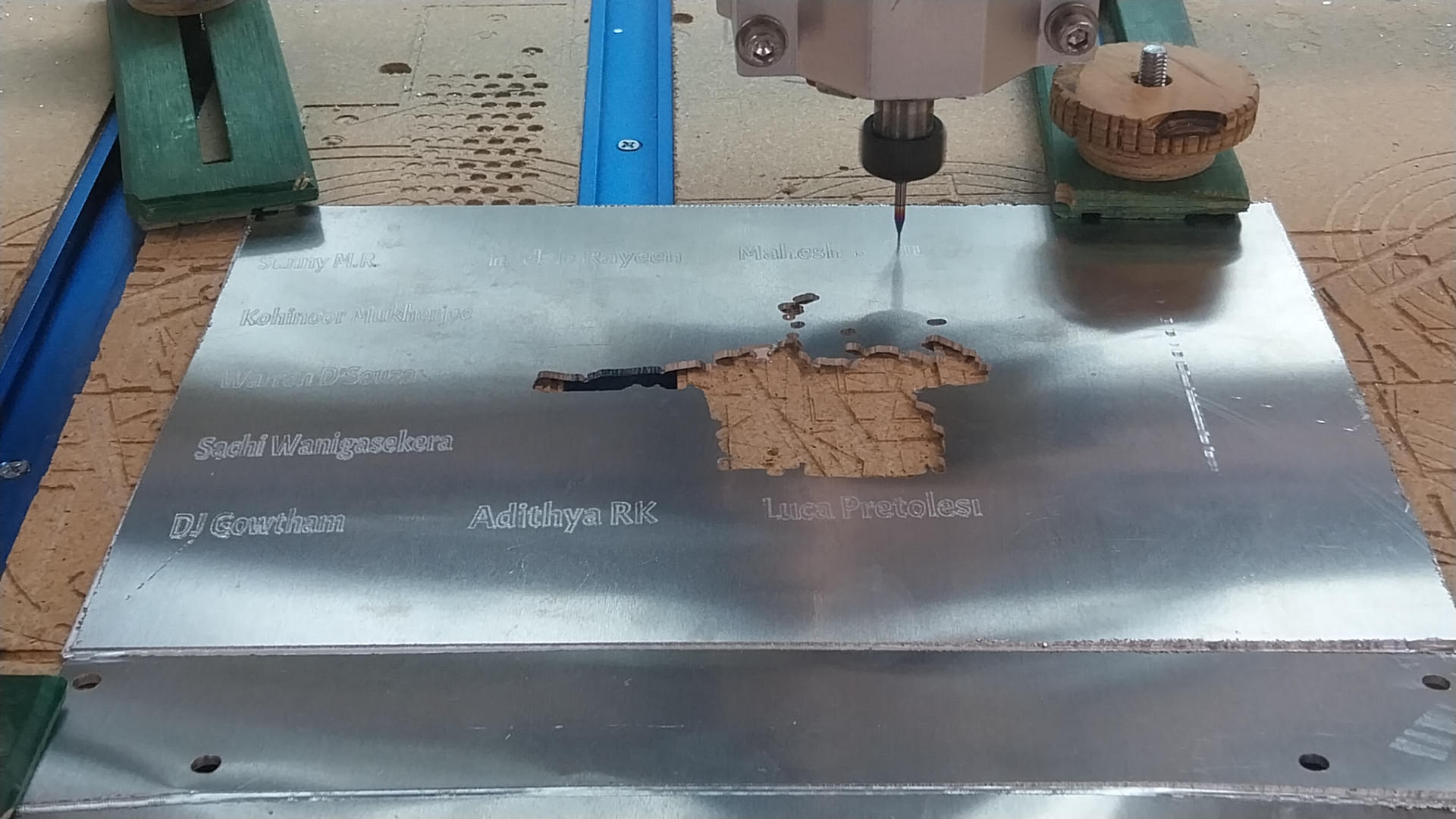

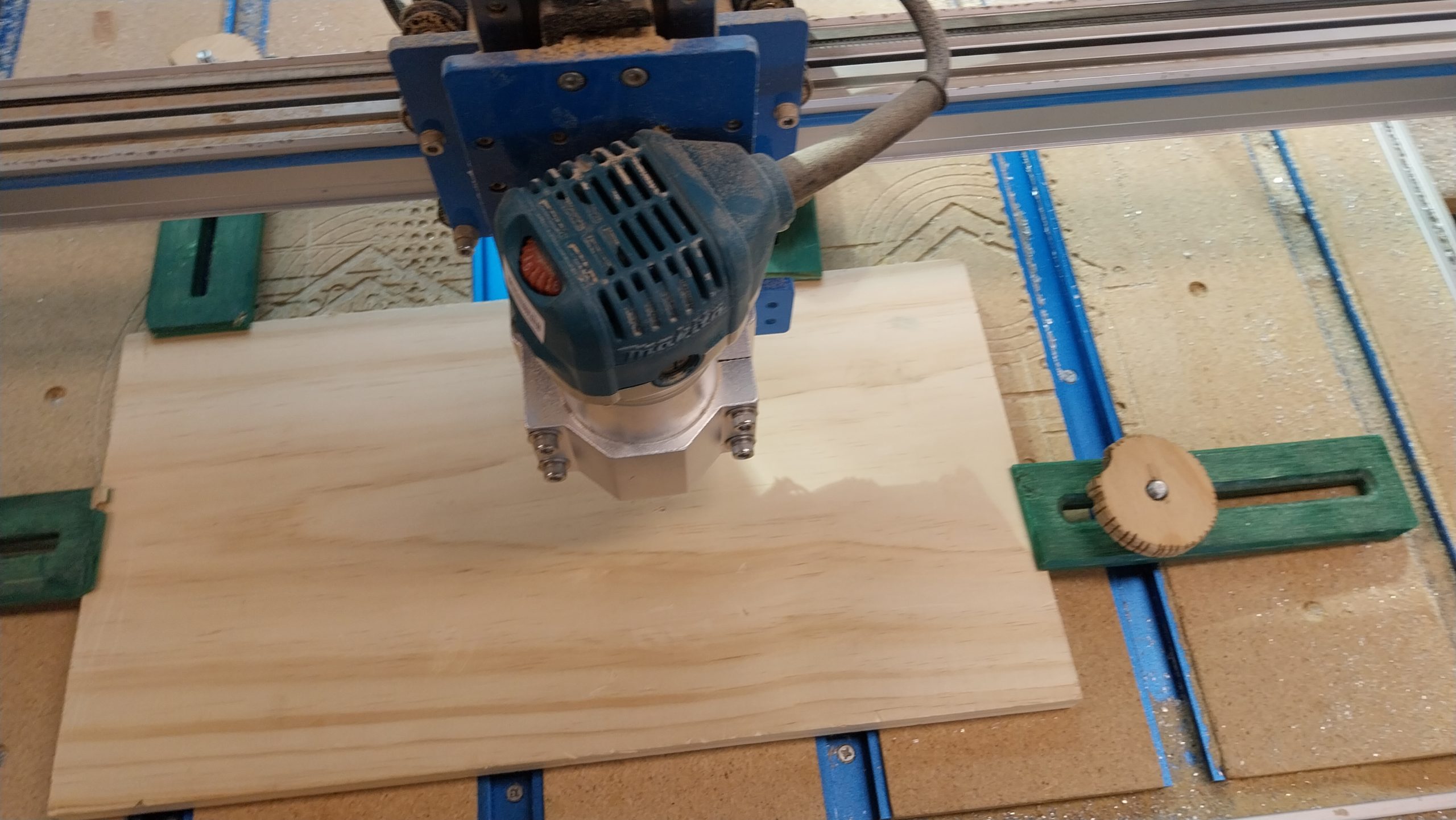
Aluminium Bending:
As the sides needed to be bent, I had to incorporate aluminum bending using techniques such as the bending press, manually bending it and making groves in the aluminium of 1mm thickness so it can. be easily bent. I origanlly decided to have all 4 sides bent, however upon realising it will be a cleaner finish and easier to implement, I decided to move forward with having only the left and right side bent with the front and back as individual pieces which are held by pop-rivet nuts that are held in place by the holdes of air cooling vents.
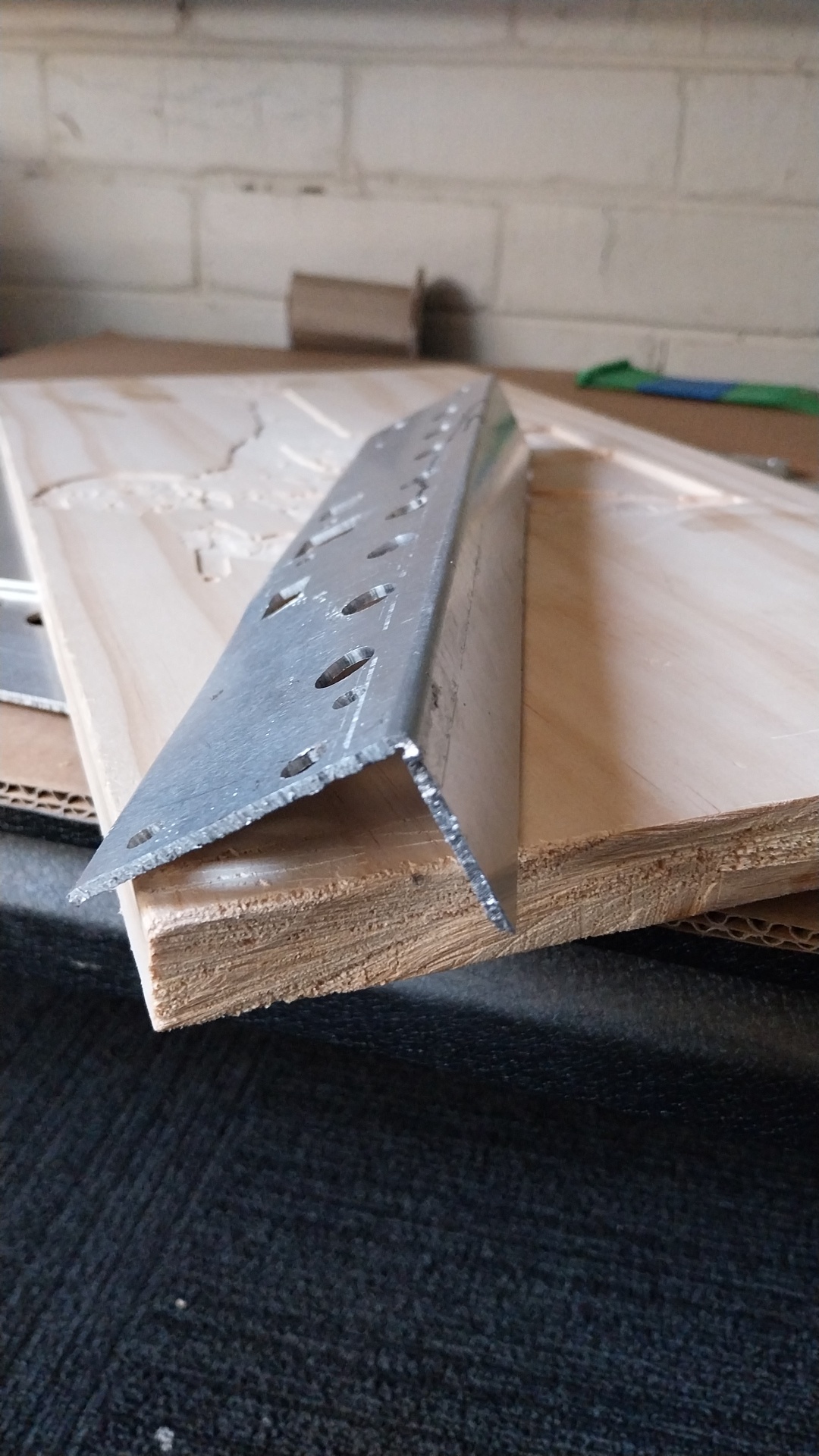
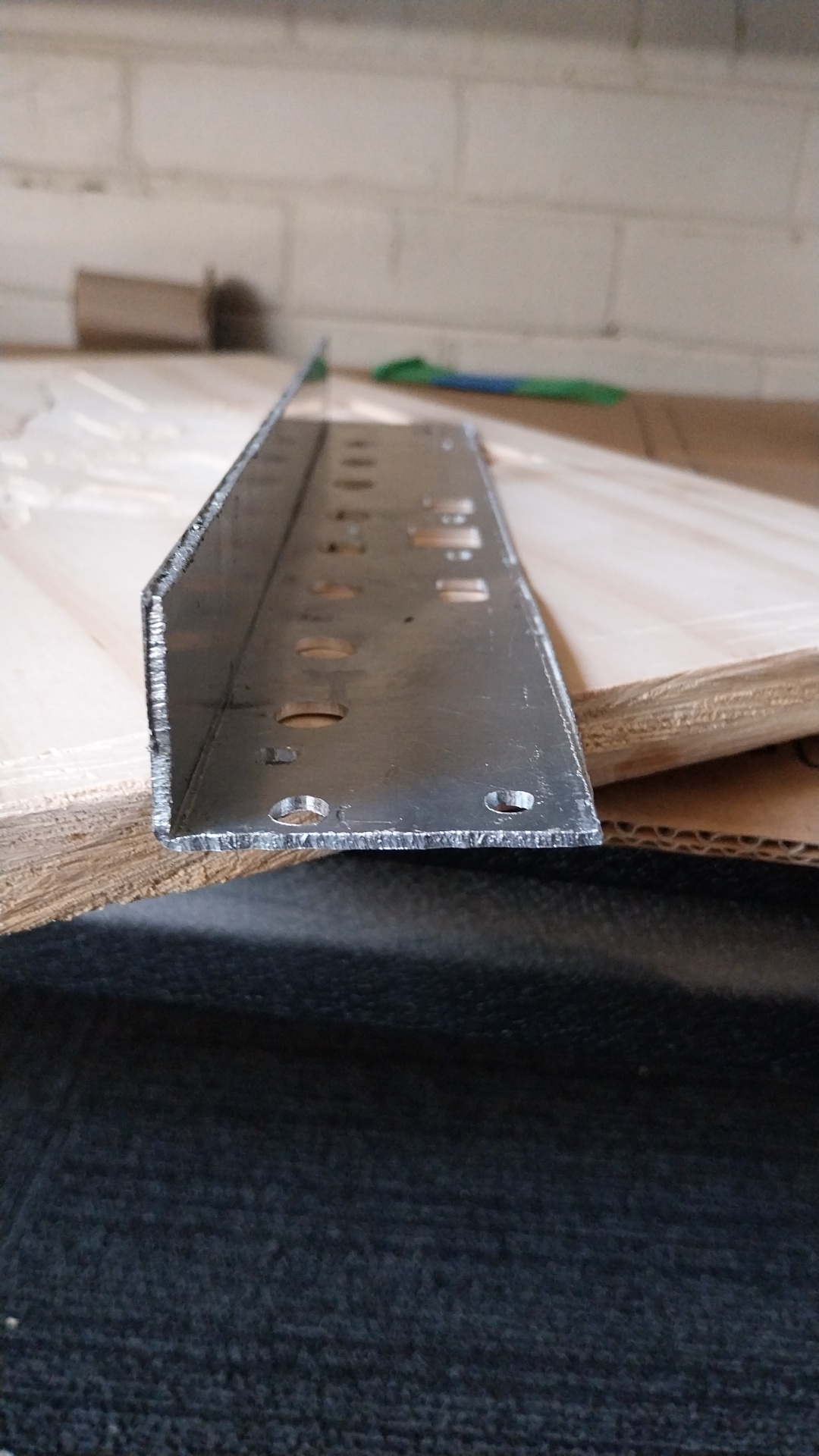
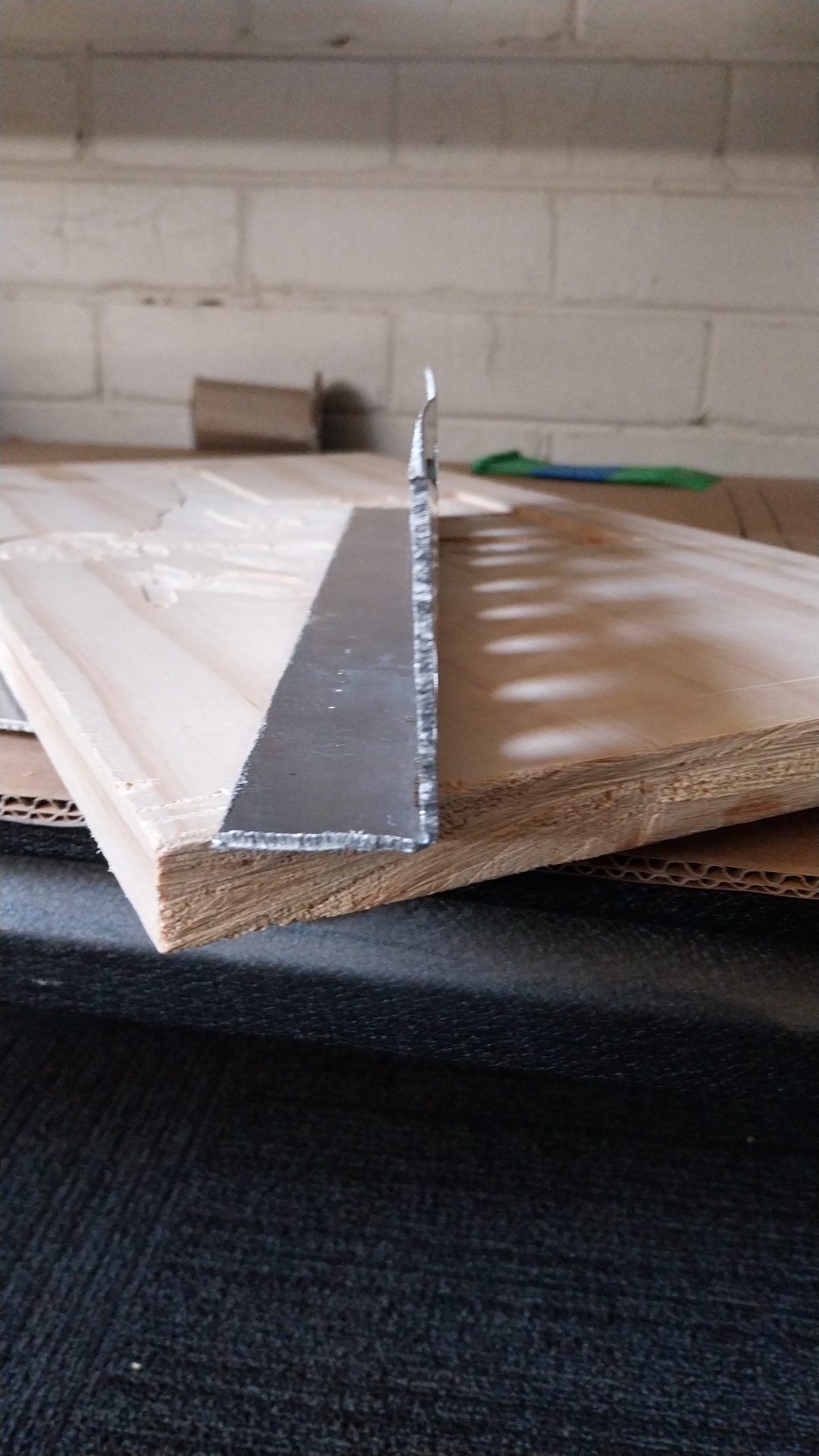
Routing Issues:
Due to the CNC router table being on an angle, the bits kept cutting through the aluminium even if the height was set correctly. This issue was fixed by manually stopping the router just about when the bits interfered with the aluminium routing incorrectly. Also, due to ultra-fast feed rates that were automatically set by Easel, over 10 aluminium CNC router bits broke as the RPM was too fast and the bits snipped. Ater discussing with the router distributor, the correct speeds were implements and eventually got the cuts accurately.
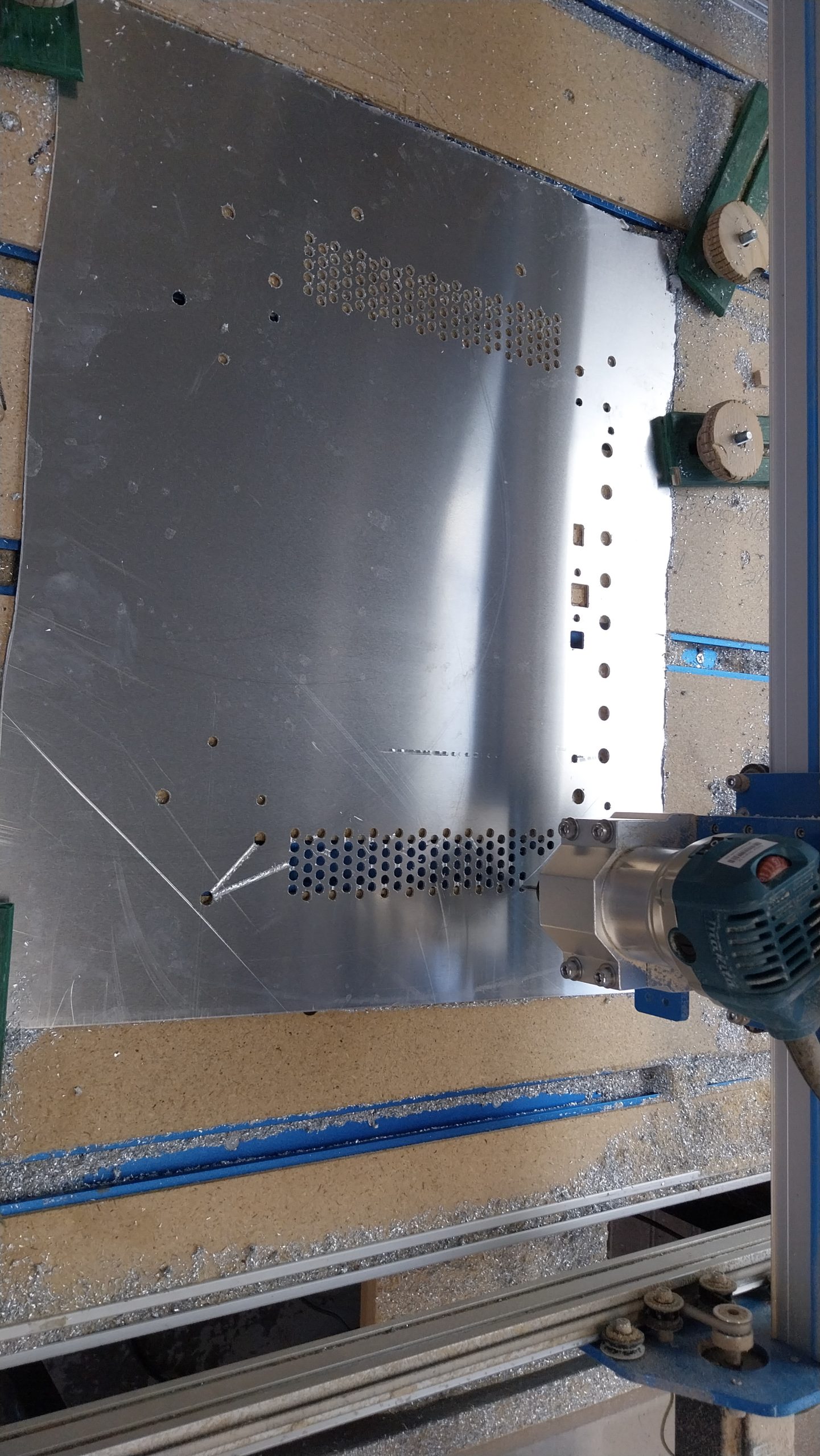
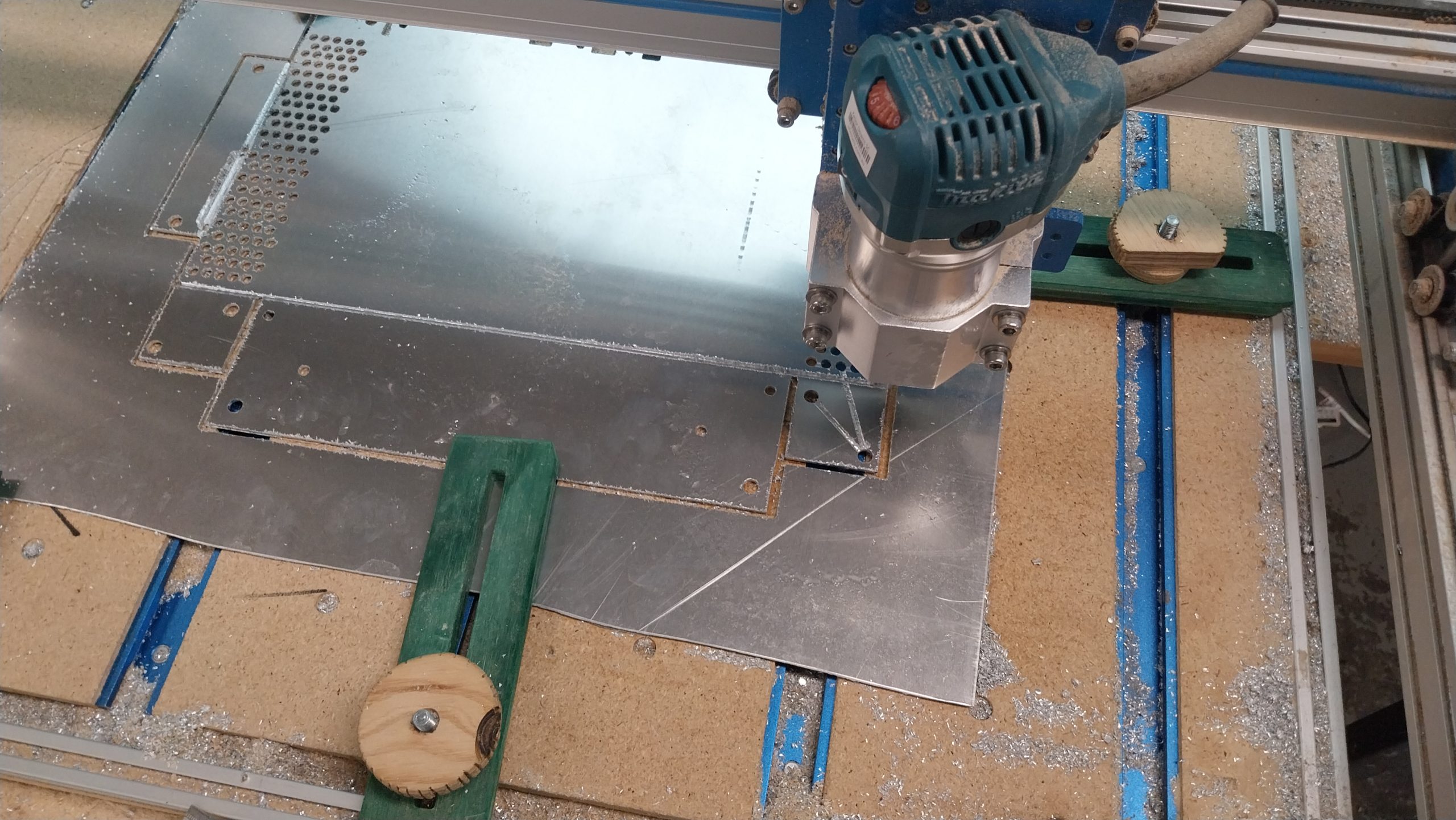
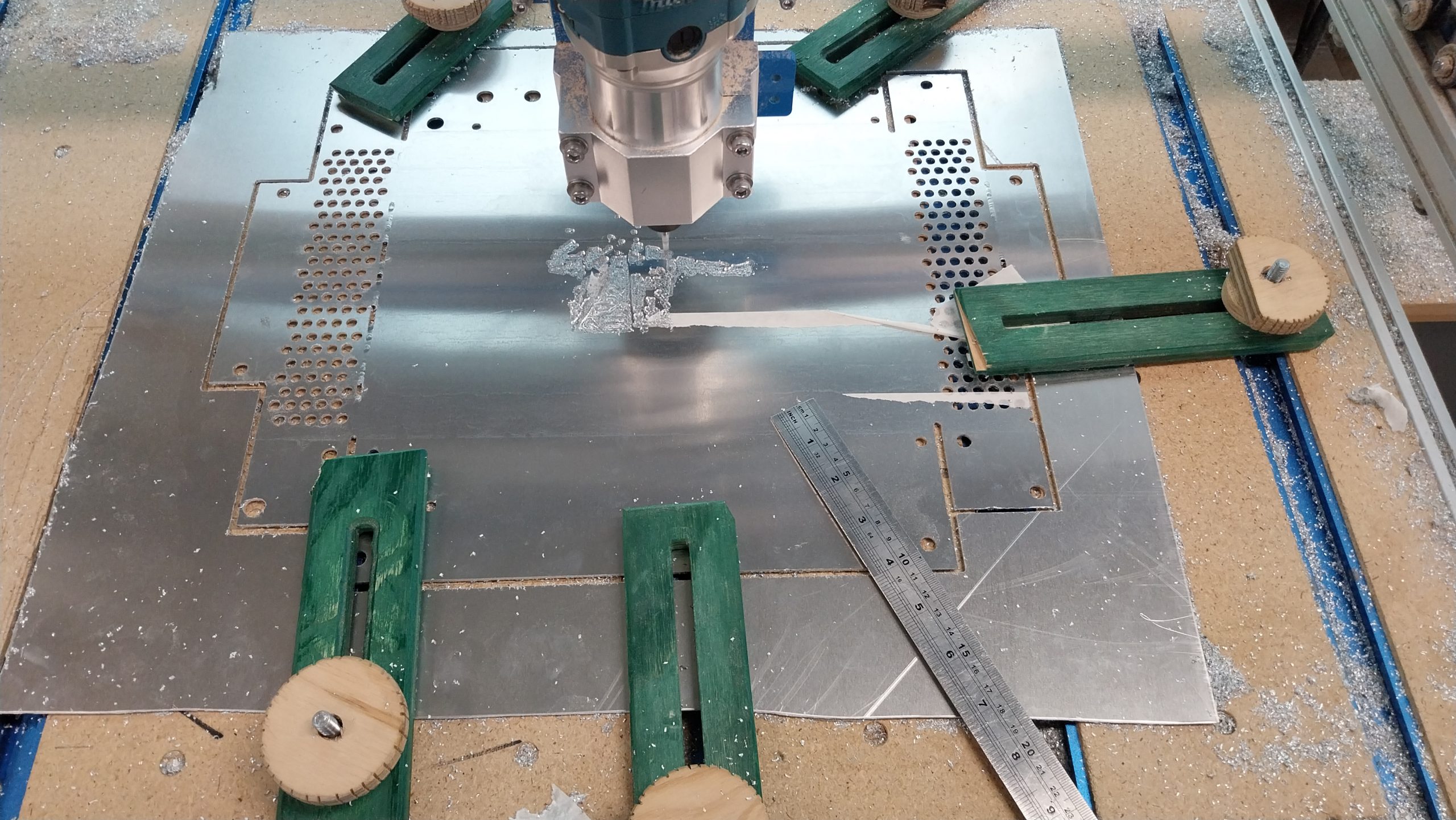

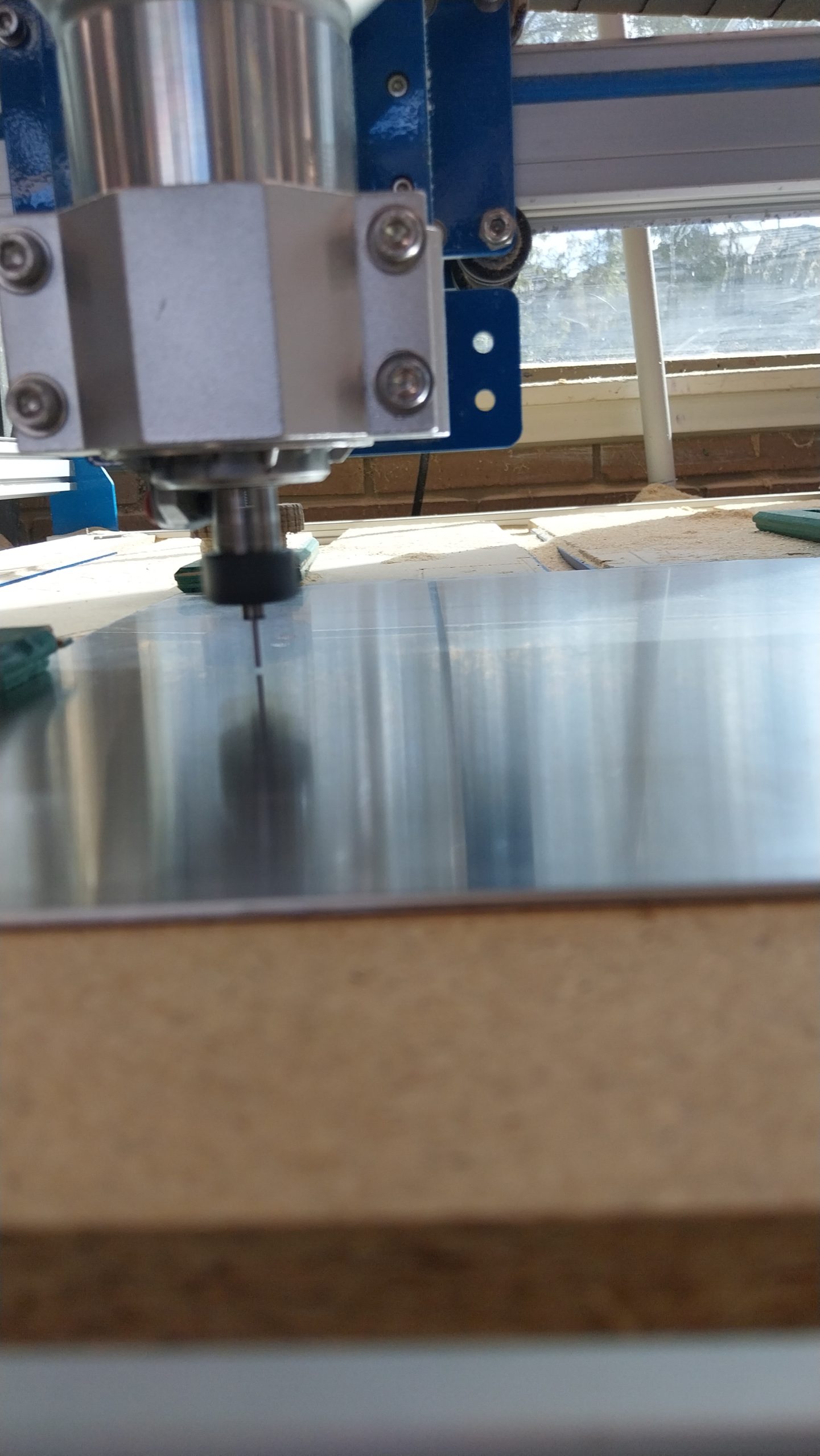
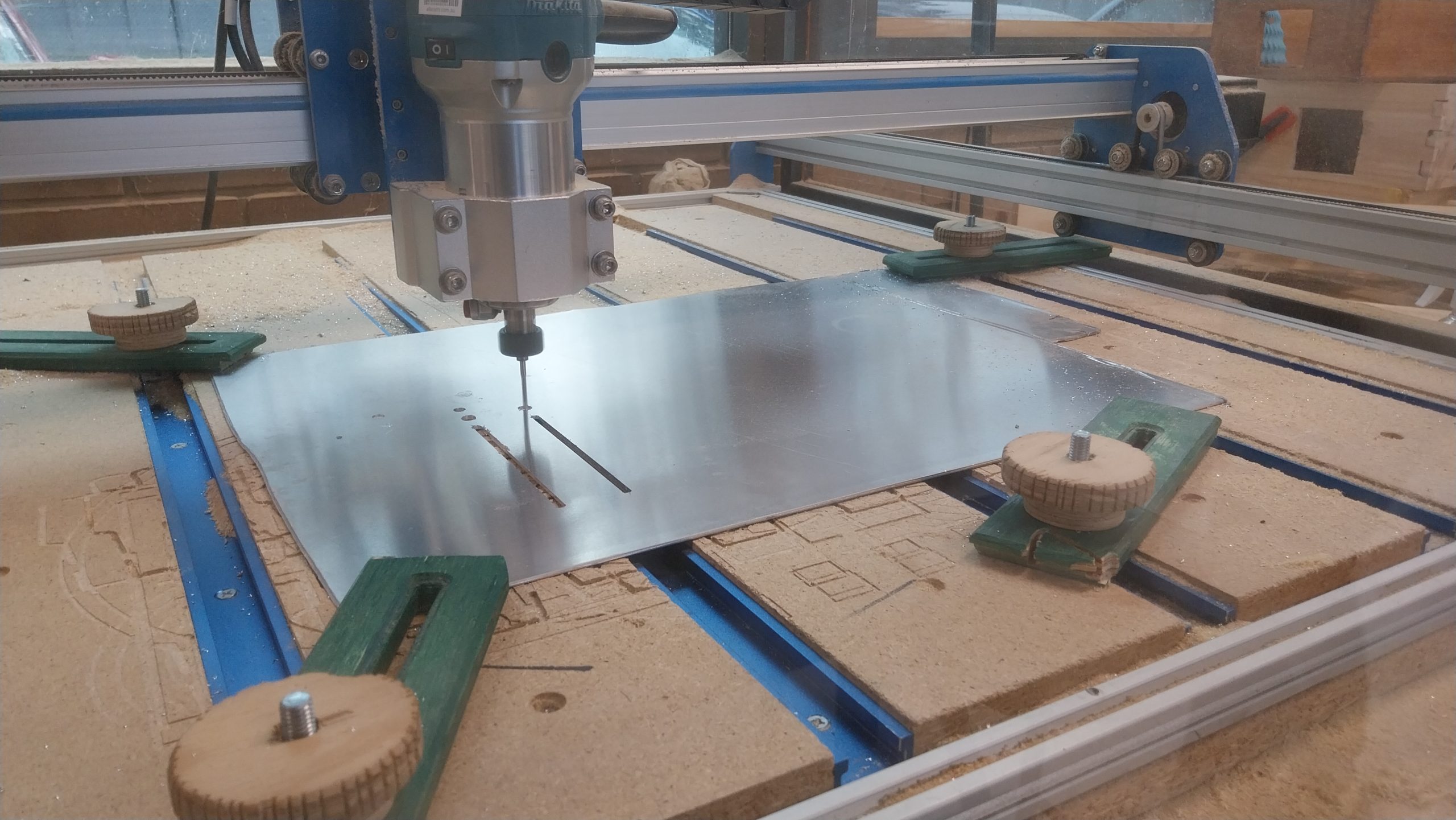
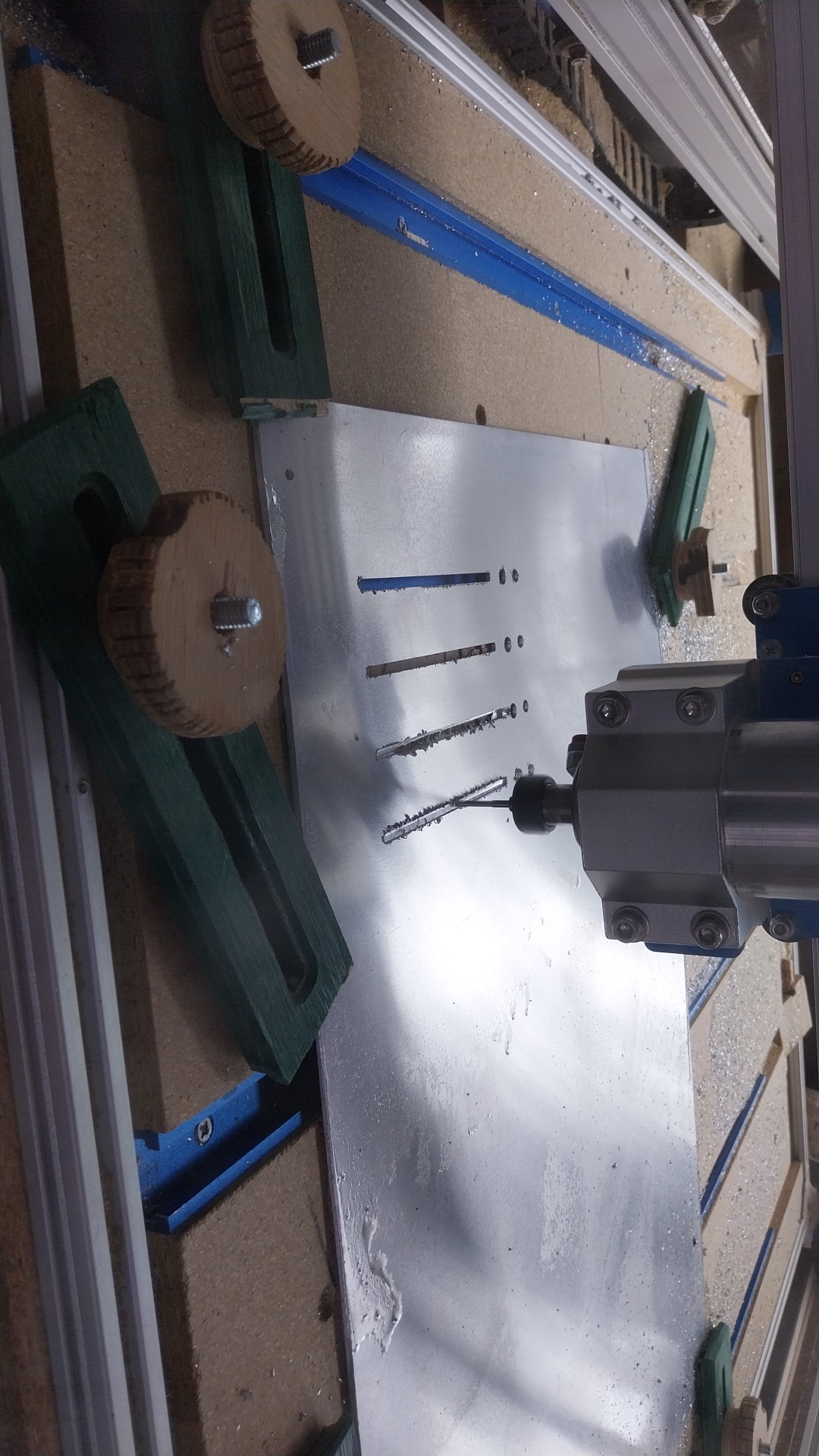
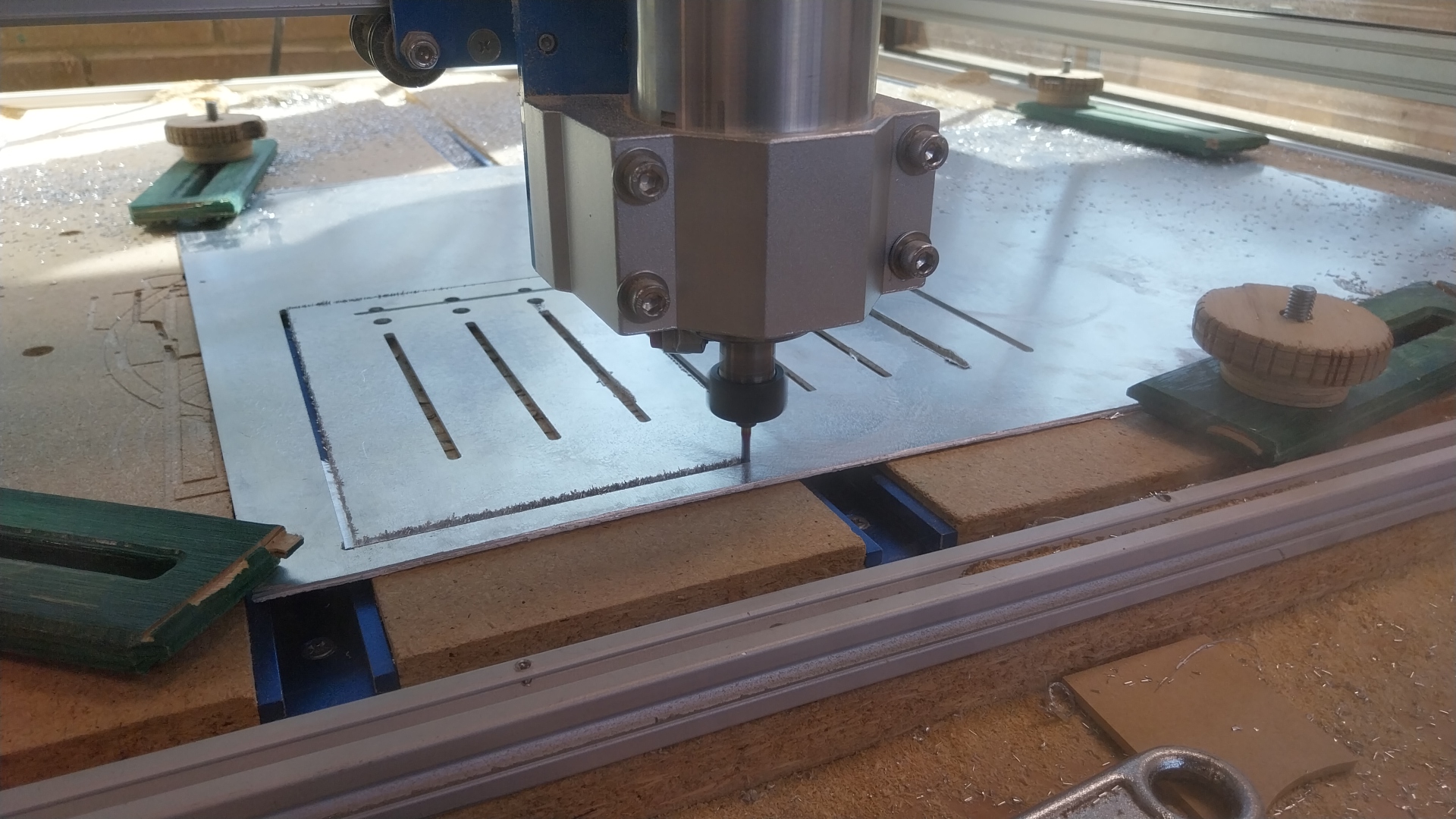
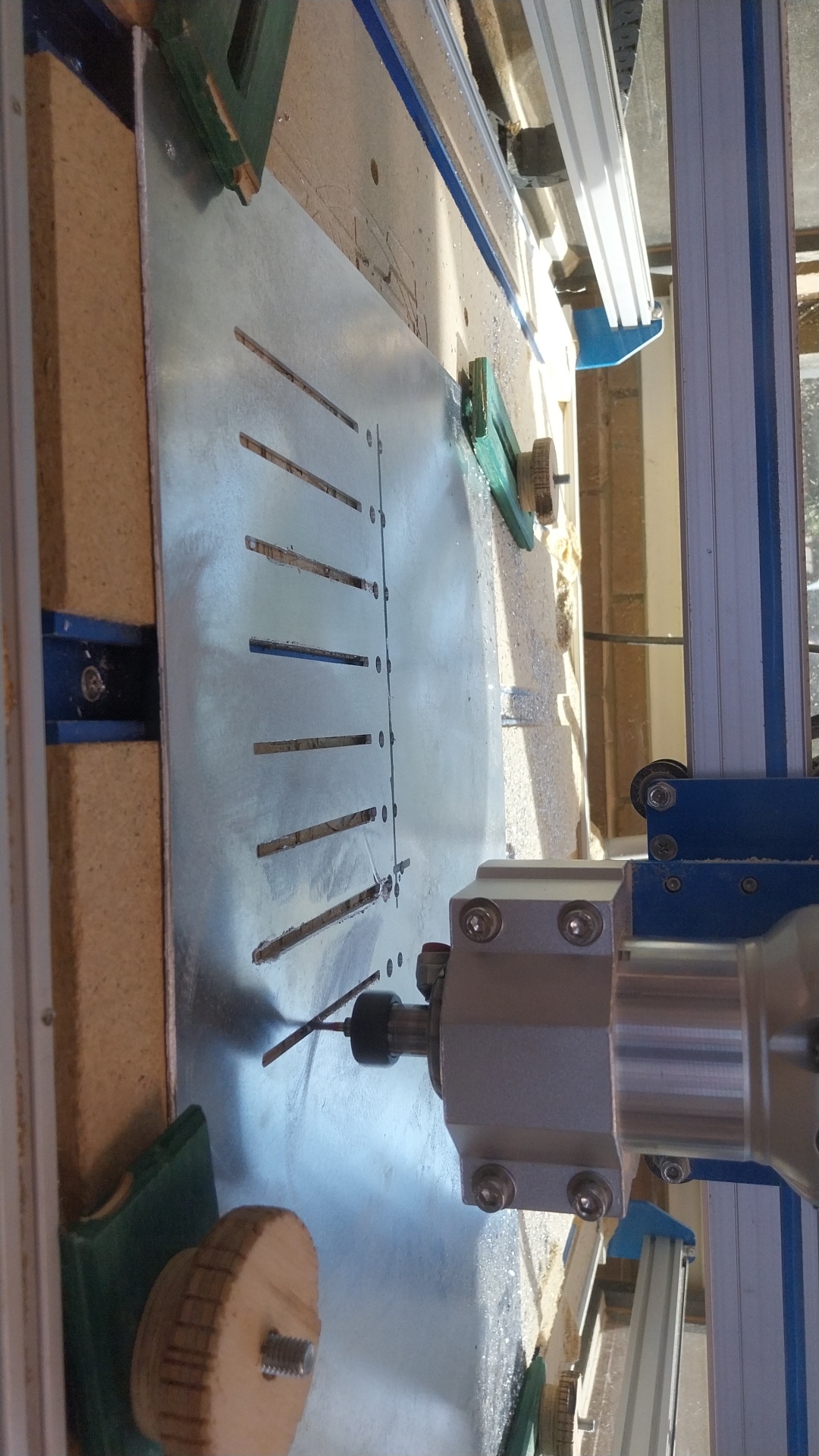